The MOVIVISION® parameterisable plant software helps system manufacturers and operators to plan, configure, simulate and start up their materials handling systems.
Setting parameters instead of programming with MOVIVISION®
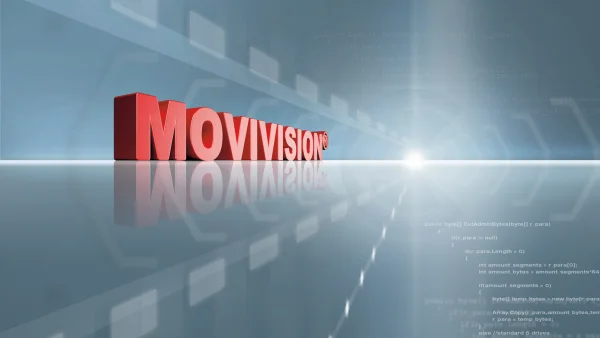
Individualised solutions and high flexibility are playing an increasingly large role in mobile and stationary materials handling technology. With MOVIVISION®, system manufacturers and operators can quickly and easily start up materials handling technology without any special knowledge of programming. MOVIVISION® combines central data management with decentralised intelligence. This simplifies and shortens the complex communication paths between all the hardware and software components.
As a result, continuous monitoring and diagnostics are also possible during production. With this flexible, user-friendly solution, retrofitting or modifying the system and performing detailed error diagnostics are no problem. MOVIVISION® offers the optimal solution for tasks from simple motions to complex coordination with three performance levels: motion, function and coordination.
Get in touch with us.
- Our experts know your industry and requirements
- Our global network ensures we are there wherever and whenever you need us.
- We have the expertise and tools to provide optimum advice and support.
Your benefits
-
Simple planning and configuration
Using the parameterisable conveyor functions in combination with virtual configuration, startup and simulation -
Simple startup
Thanks to parameterisation that doesn’t require special knowledge of programming -
High flexibility
For changes in production thanks to the intuitive operation and parameterisation -
Precise troubleshooting
With logging, simulation, virtual diagnostics, root cause resolution and external support options via VPN -
Boost productivity
With fast diagnostics, remote maintenance and simple on-site maintenance
The three steps to success: Motion – function – coordination
Features
- Visual track outline
- Integrated track visualisation and operation
- Manual operation
- Virtual pre-startup using plant simulation (2D, 3D)
- Decentralised installation with central data management
- Access authorisation management
- Automatic sequence of motion coordination (collision protection, synchronous travel)
- Ensuring independent production flows (routing management, specified targets)
- Parameterisable data exchange with higher-level controller
- Inclusion of production/part data
- Exchanging production-relevant data with higher-level systems
- Special additional functionalities thanks to technological functions (TecUnits)
- Support for safety technology
Application examples
- Single-axis applications such as roller conveyors
- Single or multi-axis applications such as rotary tables, lateral conveyors, lifting/lowering stations, conveyor trolleys
- MAXOLUTION® system solutions such as skillets with lifting tables, electrified monorail systems and automated guided vehicle systems
Functions
MOVIVISION® parameter and diagnostics tool
The user can access the central database of the MOVIVISION® server through the parameter and diagnostics tool.
MOVIVISION® server
- All data is stored in one central database
- Establishing a link to the connected decentralised control components
- Data exchange between the server and decentralised control components via fieldbuses and/or networks
- Parameters are only set or changed here
- Management and supervision of access authorisations
- Activation of automatic parameter download during unit replacement
- High degree of data security and user-friendliness
- Fault analysis option with logging
- Catalog functions
MOVIVISION® client
- Visual display of the decentralised control components’ data on the user interface
- The parameter and diagnostics data for each unit is displayed separately. Both nodes are divided into:
- Drive level
- Positioning level
- Technological level
- Option of assigning different access authorisations to users: For monitoring or parameterising, initial startup, unit replacement, etc.